没有了! Main contents of mechanical assembly
Although they have a common name called grinders, they have different prefix according to the different uses. The grinder mainly consists of the outer grinding machine, the inner grinding machine, the plane grinder, the gear grinding machine, the guide grinder, the centerless grinding machine, the tool grinder and so on. The outer grinding machine and the inner circle grinder are more common.
Main components and functions of outer cylindrical grinder
Plane grinder
Although they have a common name called grinders, they have different prefix according to the different uses. The grinder mainly consists of the outer grinding machine, the inner grinding machine, the plane grinder, the gear grinding machine, the guide grinder, the centerless grinding machine, the tool grinder and so on. The outer grinding machine and the inner circle grinder are more common.
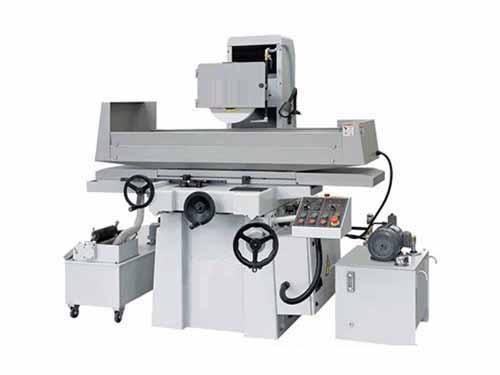
Common grinder
In order to facilitate the distinction of writing, a simple arrangement of the grinder is carried out in the model compilation method for metal cutting machine tools. Among them: M - grinder machine tool; 14 - universal cylindrical grinding machine; 32 - maximum grinding diameter is 320mm; A - the first major improvement. Keeping in mind these symbols is beneficial to the rapid resolution of the grinder. A few common grinders are described in detail below.
Cylindrical grinder
The outer grinding machine is divided into two kinds of ordinary cylindrical grinder and universal cylindrical grinder. Compared with the ordinary cylindrical grinder, universal grinder and the grinding wheel head below are equipped with rotary table, can around the vertical axis deflection angle, and increased internal grinding attachment. Therefore, the universal cylindrical grinder has more powerful function. It not only can grind cylindrical surface, end face and outer cone, but also Polish inner cylindrical surface, inner step surface and large conical cone.
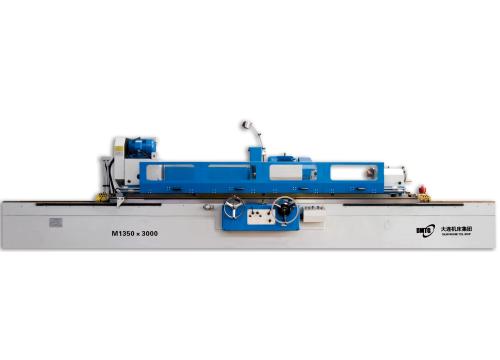
Cylindrical grinder
Main components and functions of outer cylindrical grinder
(1) the bed is used to support the components, the upper part has the worktable and the grinding wheel frame, and the inner is equipped with the hydraulic transmission system.
The table is arranged on the headstock and tailstock. The worktable has two layers. The lower worktable can move vertically and horizontally on the guide rail of the bed. The upper worktable can deflect certain angle in the horizontal plane compared with the lower worktable, so as to grind the conical surface.
The spindle headstock headstock consists of a single motor by a transmission mechanism to drive the rotation, can get six kinds of speed. The end of the spindle can be fitted with a top, a pullout plate or a chuck. The workpiece can be supported between the headstock and tailstock thimble thimble, chuck mounting is also available.
(4) the grinding wheel is used to install the grinding wheel and the grinding wheel is revolving at a high speed by a single motor. The grinding wheel rack can be used for transverse feed on the guide rail on the back part of the lathe bed. The feed method has three kinds: automatic cycle feed, quick introduction or withdrawal, and manual operation. The first two ones are achieved by hydraulic transmission.
The tail seat is used to support the workpiece.
Inner grinding machine
The internal grinder by the bed, headstock, tool frame and wheel dresser etc.. Headstock can around the vertical axis of rotation angle for grinding taper hole. The reciprocating movement of the worktable is driven by hydraulic transmission.
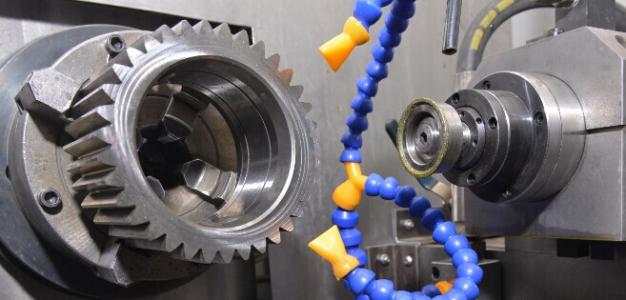
Inner grinding machine
Plane grinder
The plane grinder can be divided into two types: vertical axis type and horizontal axis type. The vertical plane grinder is grinded with the face of the grinding wheel, and the horizontal grinder grinders the plane with the circle of the grinding wheel.
The plane grinder usually consists of the bed body, the worktable, the column, the slide plate, the grinding head and the grinding wheel dresser. The rectangular worktable is mounted on the horizontal longitudinal guide of the bed, and there is an electromagnetic sucker for the installation of the workpiece. The reciprocating initiative of the worktable can be driven by hydraulic and handwheel. The grinding wheel is mounted on the grinding head, which is directly driven by the motor. The grinding head is moving along the horizontal guide of the sliding plate as a horizontal feed, which is operated by a hydraulic drive or a handwheel. The skateboard can move along the vertical guide of the column to adjust the high and low position of the grinding head and the vertical feed movement. This movement is manipulated by the handwheel.
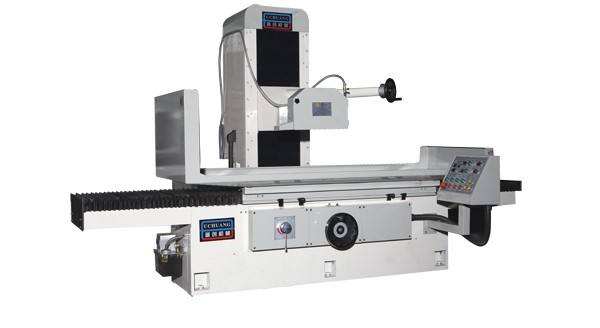